This is number three in a series of three posts on joints. Check out yesterday’s Addressing Joint Vulnerability and Tuesday’s post on Types of Joints.
Traditionally, waterstop systems have been used to waterproof joints. They act as physical barriers to block water penetration.
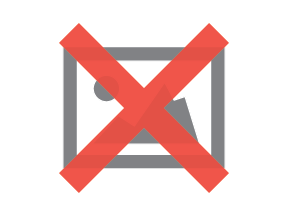
The most common, PVC, uses flat strips of high quality polyvinyl chloride (PVC) embedded in both sides of a joint to create a watertight seal. PVC waterstops are readily available in different thicknesses, widths and sizes and some PVC manufacturers offer chemical or oil resistant properties. These products can be installed in wet conditions and have a long lifespan, unlike many other waterstop systems. However, PVC waterstops pose three main challenges: they’re time consuming to install, can become easily damaged during concrete pouring and if they are damaged, there is virtually no way to tell until the joint starts to leak.
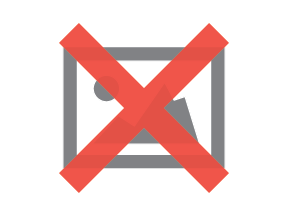
Bentonite is a swellable clay that is also frequently used to waterproof joints. It is glued or nailed in strips into joints and expands up to 16 times
in size when in contact with water. The expansion forms a compression seal that keeps water out of joints. One common deterrent from using bentonite is that it can dry out and deteriorate easily because the clay is a natural material. Additionally, it must be kept completely dry prior to installation or it will expand prematurely. Bentonite systems are also easy to displace during pouring and require extra care and labour during application.
Another joint waterproofer that is similar to bentonite is a urethane waterstop. These spongy, hydrophilic compounds swell up to three and a half times their original volume when in contact with water. But urethane waterstops possess the same drawbacks as bentonite systems – they dry up, crack and deteriorate over time; they are at risk of premature expansion if they are exposed to moisture
too early; and, they require proper placement and extra care during pouring.
Metallic waterstops are most frequently used on projects where extra strength is required or when chemical exposure is likely. They are made of steel, copper, bronze or lead and are embedded in an upright position across joints to form a continuous water barrier. The main drawback to these systems is their cost. Because they are designed for specialized applications, the material and labour costs are extremely high.
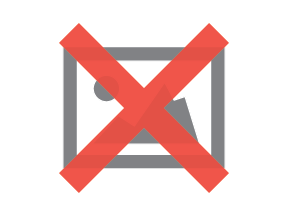
Crystalline waterstops block the movement of water through joints by growing millions of crystals within the concrete matrix. When in contact with water, the crystals grow and expand, filling the joints, capillaries and micro-cracks of the concrete. Because of the technology’s unique ability to self-seal new minor cracks even years after the initial application, crystalline waterstops provide a long term solution for joint waterproofing. As an affordable, effective and more reliable alternative to other waterstop systems, crystalline joint waterproofing systems are growing in popularity.
While concrete cracking will never be eliminated, it can be controlled and managed with effective and proper jointing practices. One of the best ways to protect your structure over the long run is to invest in a sound and reliable joint waterproofing system.