Each and every day people around the world make important economic decisions in order to be able to continue their daily lives, but something that many people do not know is that in some cases, cheap things mean higher costs.
The quote, “I am not rich enough to afford cheap things”, is a clear representation of this notion. This quote portrays that people who are not rich cannot afford to buy cheap things as they are more expensive over time. This is due to the fact that they
tend to need replacement or repair more frequently, thus higher costs.
Unfortunately, many people still misconceive and rather fail to see the expense of cheap things. The same logic and ideology can also be applied to buildings. When building a structure, there are two approaches one can take. One common option is to go by a conventional design.
A conventional design takes note of the upfront cost and tries to decrease it in order to make it correspond with the budget allocated for the project. The majority of the time, this means that lower quality materials must be used in order to reduce costs. These cuts in the quality of materials can include anything from the quality of the paint, to even indispensable aspects of the structure itself such as waterproofing system.
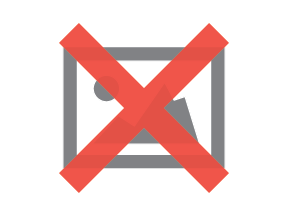
Through using lower quality materials, initial costs will be cut. Over the long run, however, maintenance costs will be more far more expensive. Lower quality materials are less durable and as a result have a lower life span. A lower life span, thus results in frequent repair or replacement costs, which will surely exceed the cost of using high quality materials in the first place. For example, someone has two roofing options, option A which is $20,000 and option B which is $30,000. While option A will only last for approximately 20 years, option B will last for about 40 years. By paying an extra $10,000, 20 years of extra service life are bought.
Furthermore, the cost per year for option A accounts to $1000/year, whereas the cost per year of option B only accounts for about $750/year. Thus, although option A may seem more appealing upfront, the more economical choice is actually option B.
Due to the drawbacks of a conventional design, a new design called a “sustainable design” has been developed to not only reduce environmental impacts but also to reduce costs over the structure’s lifespan. The primary economic goal for a sustainable design is to reduce life cycle costs (LCC) through two distinct methods. LCC is defined as the sum of all recurring and one-time costs over the full life span or a specified period of a good, service, structure, or system. As shown before, the costs of the lifetime for high quality and more durable materials are lower, and they also possess another distinct characteristic. Materials than can be later re-used or recycled, have the potential to be then sold in order to gain some of the money that went into their initial costs back. These materials are said to be taken from cradle to cradle. On the other hand, materials that cannot be recycled, or salvaged, do not possess this benefit.
Instead, they are termed as going from cradle to grave.
Because of its appealing characteristics, the construction industry has been undergoing a transition towards the development of more sustainable/green built structures. Through using a sustainable design that incorporates high quality materials, we can not only save money, but we can also reduce environmental impacts of construction.